🌱 How Asset Surveys Support Net Zero Goals in Buildings
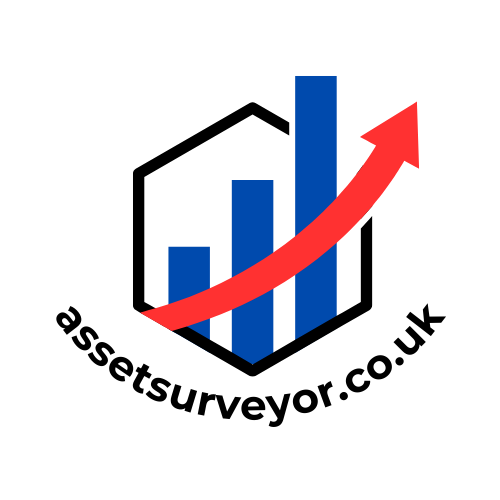
Net Zero isn’t a buzzword anymore—it’s a board-level target.And yet, many organisations still treat sustainability as a standalone project, disconnected from the
Net Zero isn’t a buzzword anymore—it’s a board-level target.And yet, many organisations still treat sustainability as a standalone project, disconnected from the
You can’t manage what you don’t know exists.And in facilities management, that lack of visibility can cost you—big. From unexpected failures to
An asset survey isn’t a one-and-done task.Just because you’ve had one in the past doesn’t mean it still reflects reality. In fact,
You might think you’ve got an asset survey.You might even have the spreadsheet, the PDF, the folder full of photos… But here’s
For any estate—whether it’s healthcare, education, or commercial property—unexpected maintenance costs aren’t just annoying.They’re expensive, disruptive, and nearly always avoidable. And 9
If you manage a building, estate, or facilities contract, there’s one question that underpins everything: Do you actually know what you own—and