🌱 How Asset Surveys Support Net Zero Goals in Buildings
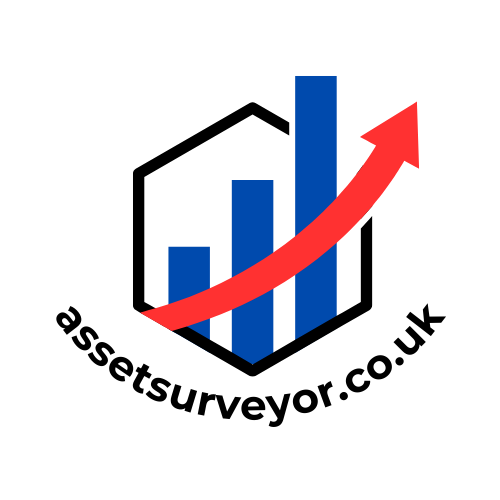
Net Zero isn’t a buzzword anymore—it’s a board-level target.And yet, many organisations still treat sustainability as a standalone project, disconnected from the
Net Zero isn’t a buzzword anymore—it’s a board-level target.And yet, many organisations still treat sustainability as a standalone project, disconnected from the
You can’t manage what you don’t know exists.And in facilities management, that lack of visibility can cost you—big. From unexpected failures to
For any estate—whether it’s healthcare, education, or commercial property—unexpected maintenance costs aren’t just annoying.They’re expensive, disruptive, and nearly always avoidable. And 9
An asset integrity framework offers a multitude of advantages to organizations across industries. It serves as a structured approach to ensure the